On the afternoon of December 9th, 2019, BWA members arrived at the Toyota Cambridge Plant to attend the half-day TPS Tour and Lecture.
Toyota began manufacturing automobiles in 1933 and has grown into the 2nd largest automotive manufacturer in the world. They have been tweaking their manufacturing processes for generations, and frankly, it shows. It is a remarkable show.
On the guided tour, very little distracts from the production process, no litter, no dust in the air, and everyone is busy working. Machines are everywhere. Robotic arms perform precision tasks in perfect harmony. Enormous automated presses stamp out car parts as they sit on specialized foundations so as not to shake the ground around them. Giant “Godzilla” machines lift car parts into overhead track systems to be bused along the production line.
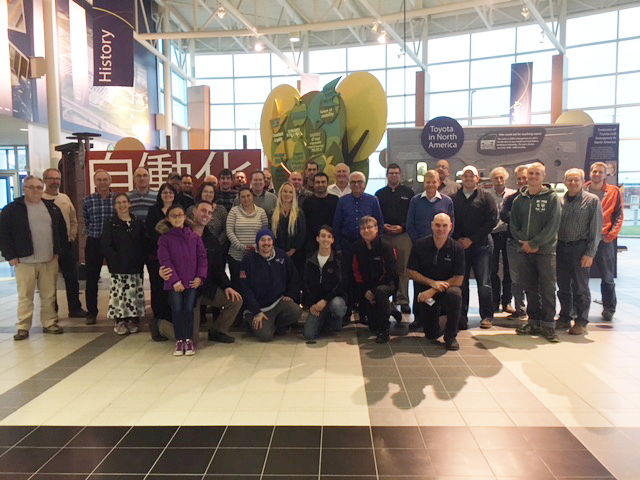
BWA organizes Toyota TPS tours throughout the year for our members, both associate and manufacturing!
Working within the machines are the team members – the most essential part of the process. At Toyota, each team member can stop the production line directly at their station. Problems are addressed as soon as they happen. By creating a culture of continuous improvements and respect for people, everyone is focused on 100% quality control with no fear or hesitation to identify a problem.
After the tour, we dove straight into the Toyota Production System (TPS) lecture, reviewing the company history and the systems they have developed to stay focused on continuous improvement. The talk flies by with plenty of opportunities to ask questions.
If you are interested in learning how TPS can transfer to other manufacturing sectors click here to view their partnership with Canada Blood Services. This is a short but sweet example of Kaizen improvements making a considerable impact.
If you have ever wondered what could look like if your company practiced Lean Principals for years on end, join us next time and see first-hand the possibilities.
To learn more contact:
Tara Davey
Program Administrator
Bluewater Wood Alliance
e: admin@bluewaterwoodalliance.com
p: 519-270-7141
Comments are closed.